Our industry-leading, high-speed industrial robots include high-payload, extended-reach, ultra-maneuverable seven-axis and unique 15-axis dual-arm robots.
Fully automatic encapsulation of automotive windows
Windows for automotive vehicles must meet a wide range of requirements. They must ensure good visibility, meet the design requirements of manufacturers and customers and function without failure for many years under extreme temperatures and weather conditions.
Decorative trims and panels must also be integrated. For this purpose, the windows are encapsulated with plastics and corresponding elements are injected for later alignment in the vehicle and for attaching additional elements. Various thermoplastics and elastomers such as PUR, PVC, TPE or EPDM are used. To ensure a bond between glass and plastic, a primer is applied to the glass areas that will later be encapsulated. The primer is a liquid medium with a limited processing time, which is thermally activated in advance. The application must be very precise, as the glass parts to be encapsulated must be completely covered with primer, but no primer may "protrude" for optical and quality reasons.
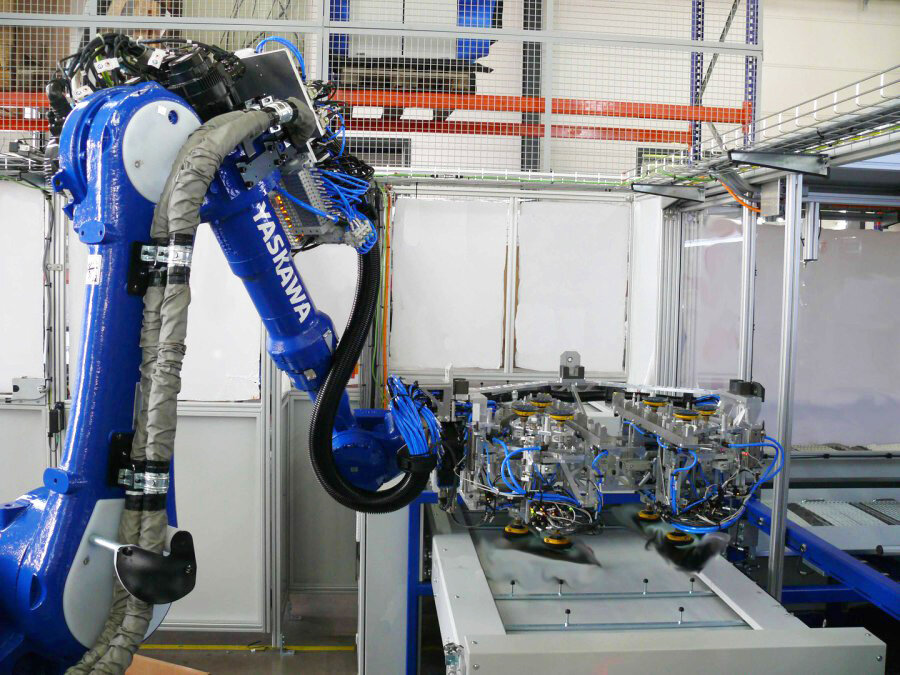
If the process is automated with robots, either the windows are guided past a stationary application tool, or the tool is moved along the previously positioned window. Various concepts, typically sponge- or felt-like moldings soaked with primer using pump technology, serve as application tools. Precise dosage proportional to the robot's application speed (track speed) is crucial.
Subsequent activation is usually carried out thermally, e. g. by hot air, infrared or UV light. Thermal activation has the positive side effect of heating the glass, which is crucial for the reliability of the subsequent injection molding process.
With the prepared windows, all the fastening parts must be inserted into the mold of the injection molding machine at the same time. This often involves different parts of different materials, shapes, and consistencies. Examples of this are pins for later positioning in the car body, clamp-like components for the attachment of trim strips and panels, as well as contour parts that are applied to edges and overmolded.
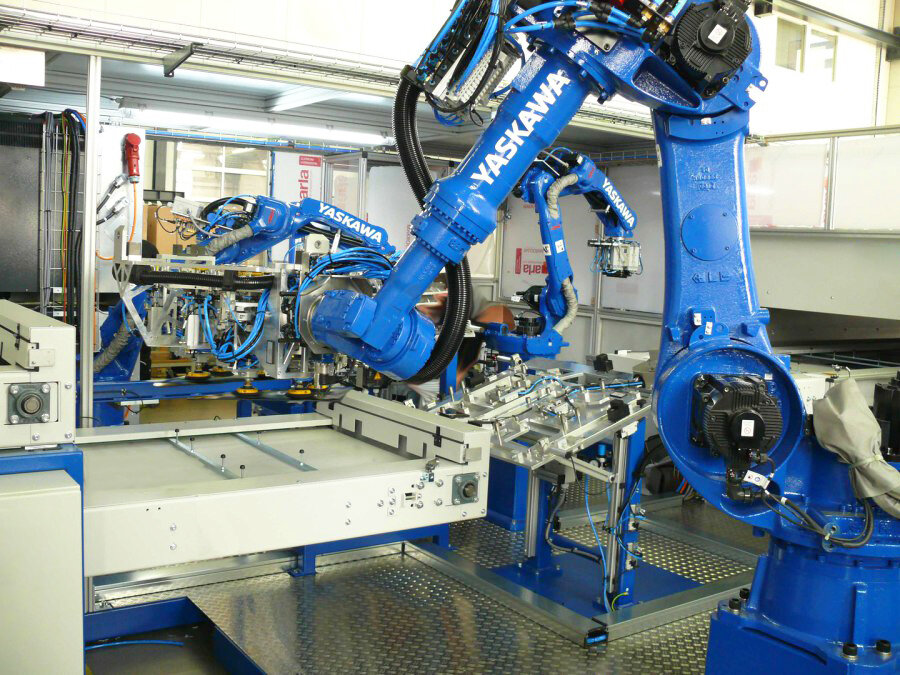
For each of these components, appropriate storage options and corresponding feeding techniques for small parts are required within the system.
All inserts required for an injection molding process, as well as the pane itself, must be provided in the later position and orientation in the mold. This is necessary to ensure that the robot loading and unloading the injection molding machine (IMM) can pick them up properly. For the pre-positioning, Robots, feeding technology and magazines are commonly used. The design and manufacture of the robot gripper for loading and unloading the machine, as well as the positioning of the parts in the mold, requires a great deal of expertise and experience.
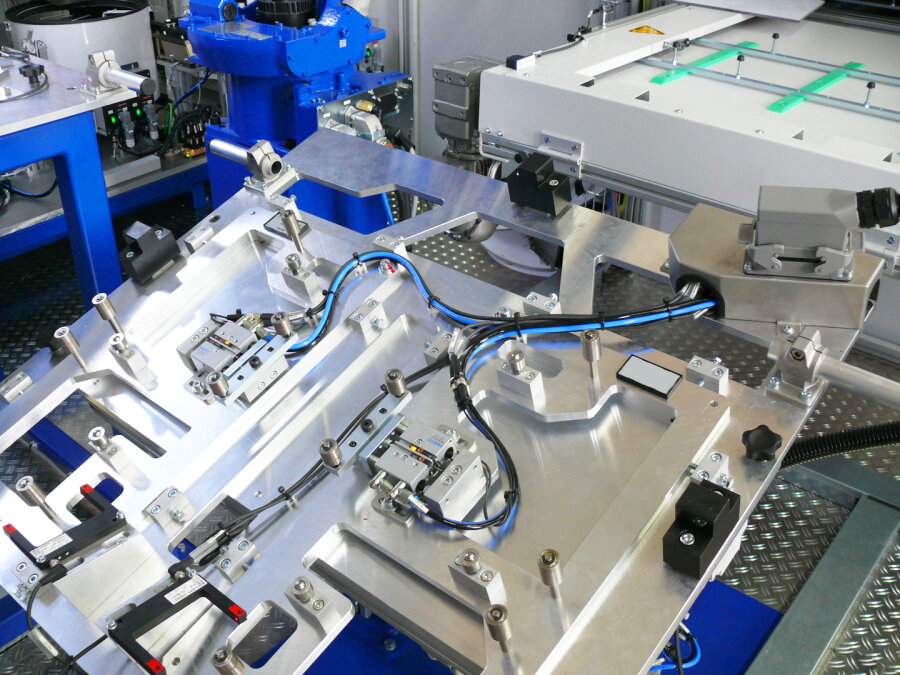
Side windows are usually encapsulated in pairs (left and right window) as a set. Additional requirements for an automation system in the automatic window encapsulation include the ability to change to different window formats and inserts. Furthermore, sufficient autonomy is required for the storage of unprocessed and finished parts, and the exact positioning and breakage-free handling of the special material glass is particularly demanding.
Text and Pictures: ©EGS Automation
EGS Automation GmbH
Raiffeisenstr. 2
78166 Donaueschingen
Germany